Variation from Rated Voltage:
In accordance with NEMA MG 1, 12.44, motors shall operate successfully under running conditions at rated load with variation in the voltage up to the following percentages of rated voltage:
- Universal motors except fan motors - plus or minus 6 percent (with rated frequency).
- Induction motors - plus or minus 10 percent (with rated frequency).
Performance within these voltage variations will not necessarily be in accordance with the standards established for operation at rated voltage.
Variation from Rated Frequency:
Alternating - current motors shall operate successfully under running conditions at rated load and at rated voltage with a variation in the frequency up to 5 percent above or below the rated frequency. Performance within this frequency variation will not necessarily be in accordance with the standards established for operation at rated frequency.
Combined Variation of Voltage and Frequency:
Alternating - current motors shall operate successfully under running conditions at rated load with a combined variation in the voltage and frequency up to 10 percent above or below the rated voltage and the rated frequency, provided that the frequency variation does not exceed 5 percent. Performance within this combined variation will not necessarily be in accordance with the standards established for operation at rated voltage and rated frequency.
Effects of Variation of Voltage and Frequency Upon the Performance of Induction Motors:
- Induction motors are at times operated on circuits of voltage or frequency other than those for which the motors are rated. Under such conditions, the performance of the motor will vary from the rating. The following is a brief statement of some operating results caused by small variations of voltage and frequency and is indicative of the general changes produced by such variations in operating conditions.
- With a 10 percent increase or decrease in voltage from that given on the nameplate, the heating at rated horsepower load may increase. Such operation for extended periods of time may accelerate the deterioration of the insulation system.
- In a motor of normal characteristics at full rated horsepower load, a 10 percent increase of voltage above that given on the nameplate would usually result in a decided lowering in power factor. A 10 percent decrease of voltage below that given on the nameplate would usually give an increase in power factor.
- The locked-rotor and breakdown torque will be proportional to the square of the voltage applied.
- An increase of 10 percent in voltage will result in a decrease of slip of about 17 percent, while a reduction of 10 percent will increase the slip about 21 percent. Thus, if the slip at rated voltage were 5 percent, it would be increased to 6.05 percent if the voltage were reduced 10 percent.
- A frequency higher than the rated frequency usually improves the power factor but decreases locked-rotor torque and increases the speed and friction and windage loss. At a frequency lower than the rated frequency, the speed is decreased, locked-rotor torque is increased, and power factor is decreased. For certain kinds of motor load, such as in textile mills, close frequency regulation is essential.
- If variation in both voltage and frequency occur simultaneously, the effect will be superimposed. Thus, if the voltage is high and the frequency low, the locked-rotor torque will be greatly increased, but the power factor will be decreased and the temperature rise increased with normal load.
- The foregoing facts apply particularly to general-purpose motors. They may not always be true in connection with special-purpose motors, built for a particular purpose, or as applied to very small motors.
Operation of General-Purpose Alternating-Current Polyphase 2, 4, and 8 Pole, 60 Hertz Integral-Horsepower Induction Motors Operated on 50 Hertz:
While general-purpose alternating-current polyphase 2, 4, 6 and 8 pole, 60 Hertz integral-horsepower induction motors are not designed to operate at their 60 Hertz ratings on 50 Hertz circuits, they are capable of being operated satisfactorily on 50 Hertz circuits if their voltage and horsepower ratings are appropriately reduced. When such 60 Hertz motors are operated on 50 Hertz circuits, the applied voltage at 50 Hertz should be reduced to 5/6 of the 60 Hertz horsepower rating of the motor.
When a 60 Hertz motor is operated on 50 Hertz at 5/6 of the 60 Hertz voltage and horsepower ratings, the other performance characteristics for 50 Hertz operation are as follows:
- SpeedThe synchronous speed will be 5/6 of the 60 Hertz synchronous speed and the slip will be 6/5 of the 60-Hertz slip.
- TorqueThe rated load torque in pound-feet will be approximately the same as the 60 Hertz rated load torque in pound-feet. The locked-rotor and breakdown torques in pound-feet of 50 Hertz motors will be approximately the same as the 60 Hertz locked-rotor and breakdown torques in pound-feet.
- Locked-Rotor CurrentThe locked-rotor current (ampere) will be approximately 5 percent less than the 60 Hertz locked-rotor current (amperes). The code letter appearing on the motor nameplate to indicate locked-rotor KVA per horsepower applies only to the 60 Hertz rating of the motor.
- Service FactorThe service factor will be 1.0.
- Temperature RiseThe temperature rise should not exceed 90 °C.
Effects of Voltages over 600 Volts on the Performance of Low-Voltage Motors:
Polyphase motors are regularly built for voltage ratings of 575 volts or less and are expected to operate satisfactorily with a voltage variation of plus or minus 10 percent. This means that motors of this insulation level may be successfully applied up to an operating voltage of 635 volts.
Based on motor manufacturers high-potential tests and performance in the field, it has been found that where service voltages exceed 635 volts, the safety factor of the insulation has been reduced to a level inconsistent with good engineering procedures.
In view of the foregoing, motors of this insulation level should not be applied to power systems either with or without grounded neutral where the voltage exceeds 630 volts, regardless of the motor connection employed.
Unbalanced Voltage On Polyphase Induction Motors
Three phase induction motors are designed and manufactured such that all three phases of the winding are carefully balanced with respect to the number of turns, placement of the winding, and winding resistance. When line voltages applied to a polyphase induction motor are not exactly the same, unbalanced currents will flow in the stator winding, the magnitude depending upon the amount of unbalance. A small amount of voltage unbalance may increase the current an excessive amount. The effect on the motor can be severe and the motor may overheat to the point of burnout.
The voltages should be evenly balanced as closely as can be read on the usually available commercial voltmeter.
Effect on performance - General
The effect of unbalanced voltages on polyphase induction motors is equivalent to the introduction of a "negative sequence voltage" having a rotation opposite to that occurring with balanced voltages. This negative sequence voltage produces in the air gap a flux rotating against the rotation of the rotor, tending to produce high currents. A small negative sequence voltage may produce in the windings currents considerably in excess of those present under balanced voltage conditions.
Unbalance Defined
The voltage unbalance (or negative sequence voltage) in percent may be defined as follows:
Percent | Maximum Voltage Deviation | |
Voltage | = 100 * | From Average Voltage |
Unbalance |
Average Voltage
|
Example:
With voltages of 220, 215 and 210, the average is 215, the maximum deviation from the average is 5, and the percent unbalance = 100 X 5/215 = 2.3 percent.
Temperature rise and load carrying capacity
A relatively small unbalance in voltage will cause a considerable increase in temperature rise. In the phase with the highest current, the percentage increase in temperature rise will be approximately two times the square of the percentage voltage unbalance. The increase in losses and consequently, the increase in average heating of the whole winding will be slightly lower than the winding with the highest current.
To illustrate the severity of this condition, an approximate 3.5 percent voltage unbalance will cause an approximate 25 percent increase in temperature rise.
Torques
The locked-rotor torque and breakdown torque are decreased when the voltage is unbalanced. If the voltage unbalance should be extremely severe, the torque might not be adequate for the application.
Full-load speed
The full-load speed is reduced slightly when the motor operates at unbalanced voltages.
Currents
The locked-rotor current will be unbalanced to the same degree that the voltages are unbalanced but the locked-rotor KVA will increase only slightly.
The currents at normal operating speed with unbalanced voltages will be greatly unbalanced in the order of approximately 6 to 10 times the voltage unbalance. This introduces a complex problem in selecting the proper overload protective devices, particularly since devices selected for one set of unbalanced conditions may be inadequate for a different set of unbalanced voltages. Increasing the size of the overload protective device is not the solution in as much as protection against heating from overload and from single phase operation is lost.
This information is based on NEMA standard MG1-14.35.
Unbalanced Line Conditions And Motor Protection
Unbalanced line voltage can be caused by at least four significant factors:
- Shunted single-phase load.
- Unbalanced primary voltage.
- Use of Delta-Wye or Wye-Delta transformers.
- Defective transformers.
Effect on the motor performance:
- Can cause serious reduction in starting torque due to low voltage in one or more phases.
- Can cause excessive and unbalanced full load current.
- Can cause nuisance overload tripping.
- Can cause premature failure of motor windings if proper overload protection is not used and known to be functional.
How to determine source of unbalanced motor current:
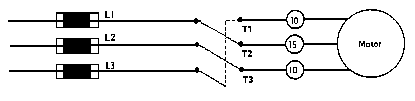
In many cases only slight variance in supply voltage may be measured, but considerable variance in motor current may be observed. To determine cause of unbalance rotate line connection to motor.
For example, T2 shows high current when connected normally. If after line-to-motor rotation T2 no longer shows high current, unbalance is in supply line.
No comments:
Post a Comment